iirc BC pipes don't have nearly enough throughput. They are slightly easier to work with but functionally GT pipes are capable of getting more fluid per second through a block than BC pipes.
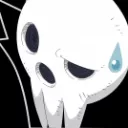
[GregTech-5][1.7.10-FORGE-1355+][Unofficial but approved Port][Stable] Even GT5 Experimental is slowly getting stable.
-
-
For the majority of the gasses and petroleum products I move around, I’m using tiny plastic pipes because they’re cheap and I don’t care too much about flow rate.
Off the top of my head, the main exceptions are steam, which requires huge volumes and which I move only short distances, water, and oxygen. For water and oxygen I use normal plastic pipes (7,200 L/sec) for the trunk and tiny pipes (1200 L/sec) for the branches.
My impression is that most mods are in the 1200-2400 L/sec range for maximum flow. Because most mods use less materials than GT, including less fluids.
Anyway, for the moment I’ve taken a break from power plant engineering and plumbing tangles and I’m prospecting for tungsten via seismic prospector. It’s been pretty tedious. I’ve found some better oil sources, but otherwise it’s mostly been ores for which I already have known sources, like iron, Oilsands, uranium, and emeralds.
Because of the ore drilling rig I’ve got a real storage problem. My main ore repository has 50,000 crushed ore in it, and I’m hand-carrying the excess to my secondary storage, which has another 65,000 crushed ore in it. Most of which I’ll probably never use.
I wish I could figure out some automated way of putting the excess into the secondary storage, but there’s no way to test for “I’ve already got a lot of that.” I guess that’s why people indulge in things like Applied Energistics or Storage Drawers. Those always felt cheaty to me, but I haven’t had such excessive storage needs before.
-
138 sites surveyed. Mostly by seismic prospector.
3 manganese sites found.
4 diamond veins.
No tungsten.
-
There is another way in getting water: you can grow cactus as ic2 agricultural crop (there will be pretty high yield if you invest some time in selection) and put them in fluid extractor.
I started a new mining site in the middle of a desert, far enough in that shipping water in from another biome didn't look much more practical than just shipping drilling fluid from my home base. So I looked into this cactus-for-water idea.
It doesn't work. IC2 crop sticks won't take cactus, it's not a valid IC2 plant. Reed is, but not cactus.
Agricraft's crop sticks, which are based on IC2's, will take cactus. But yield is the Cactus Green dye, not cactus, and it can't be extracted for water.
I tried straight vanilla cactus, harvested either with an Ancient Warfare farm, or a Forestry multifarm. The growth rate is so slow that even with a very large (16 x 16) plot devoted to cactus, the water yield is trivial. Maybe 1 L / second, about 1/1000th of the demand of a mining rig.
For the moment the site is running on imported drilling fluid, but it's slow. I need to look around to see if I have any other options (short of using an infinite water source, which is against my personal rules).
-
- Official Post
The eating plant is effectively a cactus crop, so long as you're using a new enough IC2 version that adds it.
-
Fair point about the Eating Plant. That one generally isn’t on my radar because it’s difficult to breed (no level 5-7 crops share keywords with it) the requirements are a bit stiff and awkward (lava underneath it), and ordinarily the demand for cactus is very low (dye only). I’ve got a cactus autofarm, but I don’t care that it’s only produced 300 cactus in months of play because I don’t use much.
With yield and growth 10+, I suspect it could cross the 2 cactus / second required to keep up with a mining rig, but the effort required to do so is high enough that I probably won’t explore that. It’s mostly the lava requirement, which is a PITA and potentially dangerous.
It doesn’t help that it’s not possible to test IC2 crops in creative just by plopping stuff down. Breeding a particular high-stat plant is just as time consuming in creative as in regular play.
-
- Official Post
You can at least put cactus directly onto crop sticks, so if you manage to find a desert and get some natural cactus the eating plant isn't too much of an issue to get. If you can't find cactus then you are certainly right about it being more of a pain to breed for.
The later versions do also have a command to allow giving you a cropcard of any crop with any stats you want, but that was never backported to 1.7 from the looks of things
-
NEI says that there is no such seedbag as cactus, sorry for make a confuse, maybe I've mistaken it with some other IC2 build.
On other hand if you're not going to invest in selection later in game then there's no point in this water gain method, building a pipe for even 300 blocks is way easier than that. Another interesting (but also unpromising) way is to solid down water to snow for dry transportation and liquifying it on other end. Anyway filling up GT large fluid cells is still easier and more efficient.
-
In the version of IC2 I’m playing - the 1.7.10 version, since that’s what GT5U requires - you can’t place natural cactus on crop sticks. I tried.
I’ve got plenty of natural cactus.
—-
I hadn’t seriously considered shipping fluid cells instead of using the liquid tanker. The tank car from Railcraft is typical capacity for a tank, 32 buckets for one tank. A single stack of fluid cells is 64 buckets, and a chest carries 27 stacks. It should be easy to supply enough drilling fluid via train, I’d think a couple of stacks should be enough. I’ve got a stack of steel cells (16 x 16 = 256 buckets), but I don’t know that I need them for this.
By default Railcraft prohibits carrying fluid containers in chest carts, since the capacity is almost always much higher than the tanker carts. I’m not sure if it detects IC2 fluid cells or not, since I haven’t tried. I believe it’s something you can turn off.
I think I’ll look into this. There are some headaches involved, mainly there’s no way to distinguish between chest carts carrying ore and chest carts carrying fluid cells, but I think it’s manageable and it’s far less work than laying out a pipe that runs about 6 chunks away (96 blocks) to the nearest plains biome.
-
I found tungsten. Or rather, I found the vague vicinity of tungsten.
I misplaced my seismic prospector - I found out the next day I’d stuffed it in my ore bin by accident - so I built an Advanced seismic prospector, which is EV tech rather than LV. At first it looked like a pretty amazing upgrade, since it surveys as 12 x 12 chunk area, which is 25 potential ore veins at once if you do it right. 25x the prospecting speed, for only 8x the industrial TNT. You still have to cover almost as much ground, but it’s still a lot faster.
Except that it turns out, the report gives you only that the mineral is somewhere in the 12x12 chunk area. The oilfield report gives you a simple map, but the ore report doesn’t. Ores are categorized by “near” (< 32 tiles) “medium” (33-64 tiles) and “far” (64-95 tiles). No direction, and even the “near” report is vague, since it summarizes a 4x4 chunk area, and the most-common ore can actually be spillover from a nearby chunk if the center chunk has no vein of its own.
Thus, because one report showed tungsten in the “far” ores, I know it’s one of 16 locations in a ring around the test site, but not which one. I’ll have to test each of those locations with the basic prospector.
The Advanced prospector is still a great tool if you’re looking for something specific, want to cover a lot of ground, and get a hint as to where you should look. In my first trip, I surveyed 170-ish vein locations, more locations than all of my trips with the basic prospector to combined. What the advanced prospector doesn’t do is give you a precise location, you need the basic one or mine shafts for that.
-
On a completely unrelated note, my oil distillery stalled, and I’m really not clear on what to do about it. The distillation tower always has this possibility, because it has multiple outputs. I’ve set my crude oil distillation to stop if any of 4 output hatches gets full.
What’s specifically happening is that I ran out of toluene, because I’m using it for Industrial TNT for my survey trips. My refining setup makes toluene from heavy fuel and naphtha. If the light fuel or refinery gas tanks get full, the distillation tower stops, and I don’t get any more toluene.
Initially it was the refinery gas. That gets converted to LPG, so I added a 128v gas turbine feeding into the battery that normally gets only power from the steam turbines. Initially I was only burning LPG if the steam power couldn’t meet demand over an extended period. Now I’m burning it all the time, and the LPG tank is still nearly 100% full.
Now it’s the light fuel, which gets converted to cetane diesel. Diesel powers the remote sites, acts as an alternate power source for the blast furnaces, and powers the main grid if steam power can’t keep the primary 2kV battery buffer above 50%.
I could add additional light fuel or diesel storage, and maybe additional toluene storage so that I have larger reserves. More storage usually doesn’t solve rate matching problems, but it’s possible I won’t use much toluene for a while. After all, I only used so much because I was looking for tungsten, and I kinda-sorta found that.
I could add logic to convert light fuel to toluene, but only if toluene is very low and light fuel is full. I think that’s a possible conversion, there are so many petroleum conversions I lose track. There’s already logic to convert excess toluene to light fuel, since the normal flow is Oil -> heavy fuel, light fuel, naphtha, refinery gas, heavy fuel + naptha -> toluene, toluene -> light fuel, light fuel -> cetane diesel.
-
Soon there will be no such problem as excess LPG for you, tungsten sintering and alloying are those full-time HV/EV processes I mentioned before and you're going to need it much from now on
Display Spoiler
Now, when I look back at my path it's obvious that all that time I spent on tungsten processing could be much less if I were to build additional EBF and power generators early. Now I feel it's time spent in vain in one sense.
-
I've been having some issues with oil distilling too, I've rebuilt the whole setup a couple of times and just ended up burning almost all of the products and "voiding" the energy making cobblestone because the storage would just keep getting full and blocking everything. With so many different outputs it's impossible to keep things balanced.
Also, looking at the recipe for the fusion reactor controller, I regret switching my 2 reactors to thorium
since it requires *some* plutonium, unless I've missed something.
-
It's 45 plutonium in average, not so much at all. At the moment you consider building fusion reactor this is nothing compared to other requirements (without spoiling a recipe, for example: 16 stacks of chrome, 512 superconductor wires and most of all the very controller), there are long way ahead, you can just make required amount of plutonium in replicator or reactor many times.
On the other hand is 12 stacks of lutetium that you will need eventually.
Also I didn't agitate to switch to thorium completely, it's up to you in the end. I just promoted nuclear technology and described the benefits of using it.
-
Turns out there’s no simple light fuel -> toluene conversion. Water cracked light fuel produces heavy fuel and naphtha, and steam cracked light fuel produces heavy fuel and toluene, but there’s no direct single-block distillery recipe for light fuel -> toluene.
For the moment, I’m going to let it slide, since I surveyed the precise location of the tungsten, and I’m not in dire need of iTNT immediately. The problem may resolve itself when I set up a heavy fuel cracking setup, or high octane gasoline synthesis. Light fuel cracking is very far down my list, particularly since it produces products I can’t use right now.
I did a little re-wiring of my power grid, so there’s now a 2kV trunk feeding several HV branches, rather than the 2kV battery feeding almost directly into a single HV transformer which feeds the rest of the base. I was having power distribution issues. Immediately after wiring it my consumption went from 2000 EU/t (the limit of the 4 amp HV line) to 3000.
Distilled water destruction under continuous load continues to be a problem. I may add a 3rd distillery producing water for that system, though the amount of power I’m using for that is starting to feel excessive. It’s eating most of the power increase I got for switching to large turbines.
-
It doesn't seem to have been mentioned before, but are you sure you didn't build your boiler across chunk borders? Wiki says that it can lead to steam/water loss.
Another option is to build a small two-layer distillation tower for fast and efficient water distillation.
After all, if dist.water/steam system doesn't work as closed one, you can go back to using regular water since it's a boiler and not an LHE.
-
Yes, I’m sure that I didn’t build my boilers across chunk boundaries. I use NEI’s F9 option to verify that before building any multiblock machine. That doesn’t fit the observed behavior anyway - if the steam was vanishing, the turbines wouldn’t run, and I wouldn’t get power.
It’s fairly clearly a bug in boiler startup, because it behaves properly once the boilers are running. It’s consistent with the idea that the boiler eats fuel and water at 100% while heating up, but only produces a fraction of its rated steam output while heating. Overall efficiency is about 30% during heating according to the wiki.
For a titanium boiler that means 17,000 L of water per boiler gets eaten without producing steam, each time the boiler starts. That’s roughly the loss I’ve observed, though I haven’t measured it properly in Creative yet.
Switching back to regular water is unworkable. I built the large turbines originally primarily because boiler water consumption was a serious problem. That it increased efficiency and improved power output was secondary. Two titanium boilers eat 426 L/sec of water, and my water collection was not keeping up over the long run.
I’ve since throttled the 2nd boiler, so they’re collectively producing 55,000 L/sec of steam instead of 64,000, or only 1000 L/sec more than the turbine consumption. This means that the net consumption of the boilers is 7 L/sec distilled water. A single 128v distillery produces 12 L/sec of distilled water, so the distilleries are easily keeping up now.
I calculate it’s costing me about 2 million EU to replace the lost water per boiler startup. If the boilers run once while filling the 20 million EU buffer, that’s a 10% loss. Under continuous load it drops to less than 1% as the boilers run for a long time between starts.
I haven’t looked at the cost of distilling water in a distillation tower vs. the single-block distillers. I think of distillation towers as being large and expensive, it didn’t cross my mind that a water version is only 2 blocks high. Still very expensive compared to a couple of 128v distilleries, but maybe worth doing anyway.
-
Just tested it. Well, it's actually 3 blocks high because it's minimal height for tower to form, while tecnically height determined by recipe and it must be 2 for d.water.
-
Hah, there’s a post mentioning this issue in the Support thread, and Greg acknowledges that the large boiler eats water while heating up while producing no steam. Of course, he’s almost certainly talking about GT6, not GT5U, but I wouldn’t be surprised if it’s the same overlooked issue.
I still need to test it to verify the numbers.
-
- Official Post
actually my boiler doesn't eat steam while heating up, it does while cooling down. Different cause, same effect of voiding Steam to preheat the thing.
-